Analytical Methods - Black gloss pottery
Black glass pottery
The MedConTaCCt project integrates archaeological analyses and archaeometric research in order to develop a more accurate way to classify ceramics and to relate them to their areas of provenance. At the same time, the study of the manufacturing process is in fact a procedure of reverse methodology that will provide a scientific explanation about how to classify the pottery in one way or another. Our specific objectives are:
- Identify meaningful ceramic chemical groups present in the samples analysed.
- Compare the analytical results with the macroscopic classifications realized by the archaeologists, which have traditionally resulted in the following groups: Campanian A, Campanian B (Etrurian), Middle Cales, and Late Cales.
- Identify their provenance and provide information on the technology used for their production in terms of selection of raw materials, application of glosses and firing temperatures.
- Relate the meaningful ceramic chemical groups identified by archaeometric research with their archaeological contexts in their settlements and organize them chronologically.
- Compare the provenance of the ceramics under study with those from previous studies in order to gain a clearer idea of the trade networks between the Italian Peninsula and northeastern Hispania, taking into consideration north Italian and south Gaulish sites as well as the cargo of at least one shipwreck.
Technical processes to manufacture Black Gloss Pottery
The use of clays with low calcium content at the beginning (Campanian A) and clays with rich calcium content for the elaboration of Campanian B and C categories, although the recipe for the preparation of the pastes can vary from one workshop to another, is the first step in the elaboration of Black Gloss ceramics. Before firing, the process is completed by applying a fine particle size barbotine made from an illitic non-calcareous clay on to the paste in order to obtain a shiny and waterproofing gloss. Finally, a firing process involving an oxidation phase up to 800 ºC, reduction to a maximum of 900-950 ºC and an oxidation cooling process, will produce the intended product.
ANALYTICAL METHODS
Chemical analyses (provenance studies)
Step 1: The superficial layers must be mechanically removed, and the samples must be milled in a tungsten carbide cell mill Spex Mixer mod. 8000.

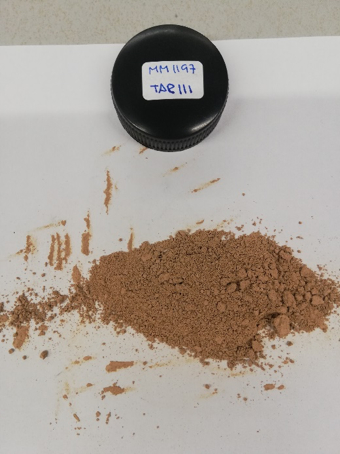
Step 2: The powder must be dried in an oven for 12 h at 105 °C. To avoid rehydration, the samples are kept in an environment with controlled temperatures and humidity during the entire process of preparation of glass bead and powder pearls.
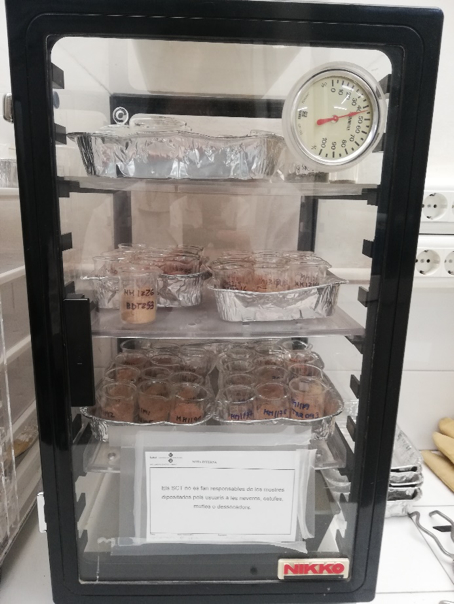
Step 3: To determine major and minor elements, two 30 mm glass bead replicas were made by mixing 0.3 g of dried sample with 5.7 g of lithium tetraborate (Li2B4O7) flux (1/20 dilution) and 5 mg of lithium iodide (LiI) release agent.
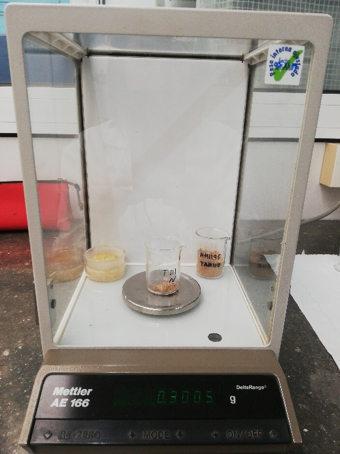
Step 4: This mixture is homogenized and deposited in a 95%Pt-5%Au crucible and melted in a fully-automatic bead preparation system PANalytical Perl'X-3 at a temperature of 1125 °C.
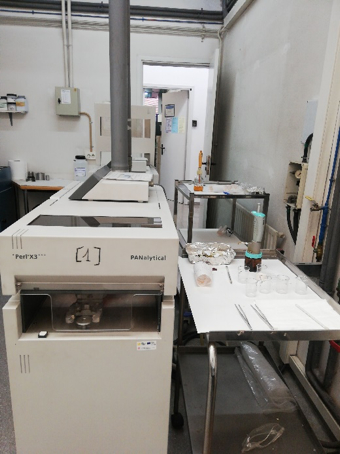
Step 5: To determine trace elements, pressed powder pellets were made using 6 g of sample mixed with a 2 ml binding agent solution of n-butyl methacrylate synthetic resin (Elvacite® 2044) in acetone at 20 % by mass. This mixture was manually homogenized in an agate mortar to dry out and placed on a base of boric acid (H3BO3) in an aluminium vessel of 40 mm diameter that was subjected to a pressure of 200 kN for a period of 60 s using a Herzog press.
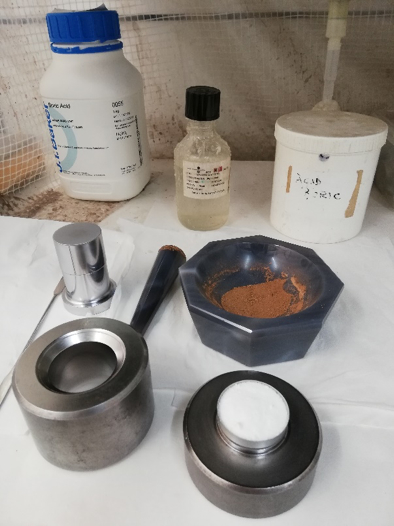
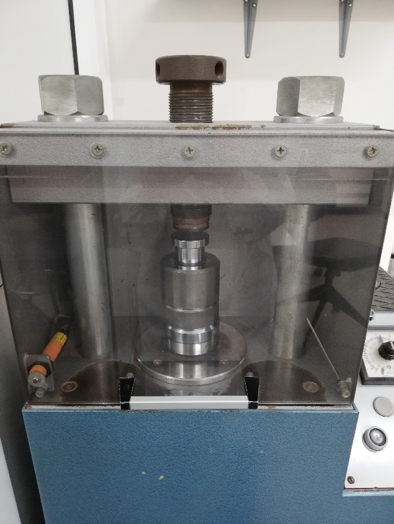
Step 6: The quantification of the concentrations was performed using an AxiosmAX-Advanced PANalytical spectrometer with a Rh excitation source calibrated by a suite of 56 international Geological Standards. Interferences were taken into consideration and matrix effects were corrected by using the PANanalytical Pro-Trace software for trace elements. The elements determined were: Na2O, MgO, Al2O3, SiO2, P2O5, K2O, CaO, TiO2, V, Cr, MnO, Fe2O3 (as total Fe), Co, Ni, Cu, Zn, Ga, Rb, Sr, Y, Zr, Nb, Mo, Sn, Ba, Ce, W, Pb and Th. Major and minor elements are given as concentrations of oxides in percentage by mass (also referred to as wt %). Trace elements are expressed as concentrations of elements in μg g-1(or ppm —parts per million).
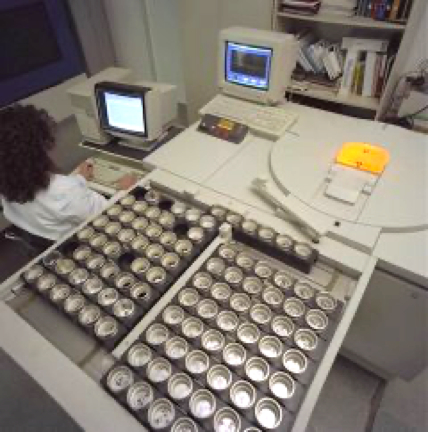
Step 7: Finally, loss on ignition (LOI) was determined by firing 0.3 g of dried specimen at 950 °C for 3 h. Calcinations were carried out in a Heraeus muffle model M-110, by using a heating rate of 3.4 °C min-1 and free cooling.
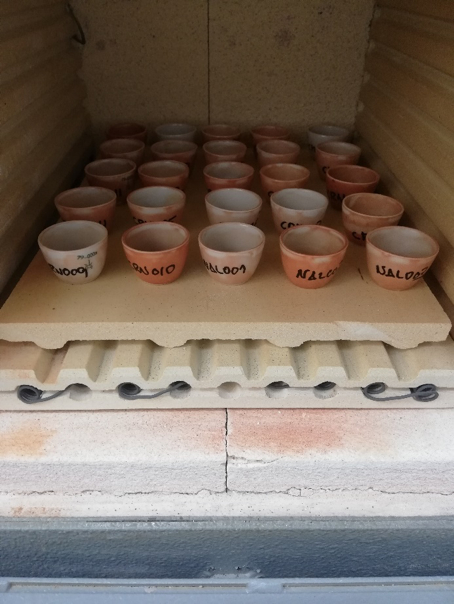
Loss on ignition (Pérdida al fuego – PAF). This value detemines the total amount of water in the composition (H2O), hidroxile groups ((OH)-), and volatile compounds contained in the analyzed sample, such as CO2 from carbonates. All of these elements are lost as the firing temperature is increased. Given that the various samples, although they belong to the same production, may be fired at different temperatures, individuals with the same composition may present differences in the PAF value. The decrease in PAF occurs as the firing temperature increases, and implies an apparent increase in the same proportion of all the other components mentioned, producing differences in the chemical composition between samples with the same composition without having their clays a different origin.
Chemical results must be statistically treated for their correct interpretation. There is a solid methodological and theoretical foundation on compositional data studies and their statistical treatment (initially the studies of geologists together with statistics, especially those developed by Aitchison during the 80s and the beginning of the 90s and after that, by Buxeda the one we follow in our research). When looking a composition, the elements chosen are those probably found in the materials analysed, forming part of that composition. Since we are working with pottery and pottery is made up of clays, we chose the elements that are more likely to be found in the clays selected for making pottery (illite is one of the most important components in ancient pottery as are kaolinite, chlorite and smectite). In addition to the above, trace and minor elements are essential. Chemical analysis is not just a matter of grouping samples; our goal is the bulk chemical analysis, which helps both to group samples and to get closer to the actual composition of the raw materials used in the fabrication of pottery.
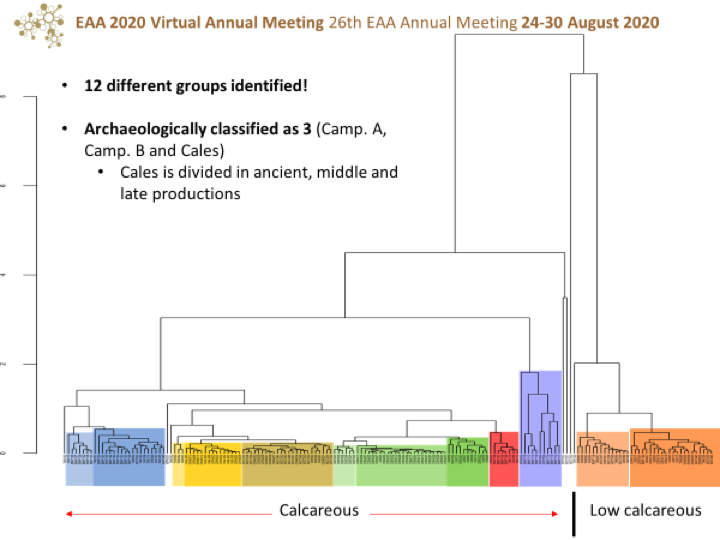
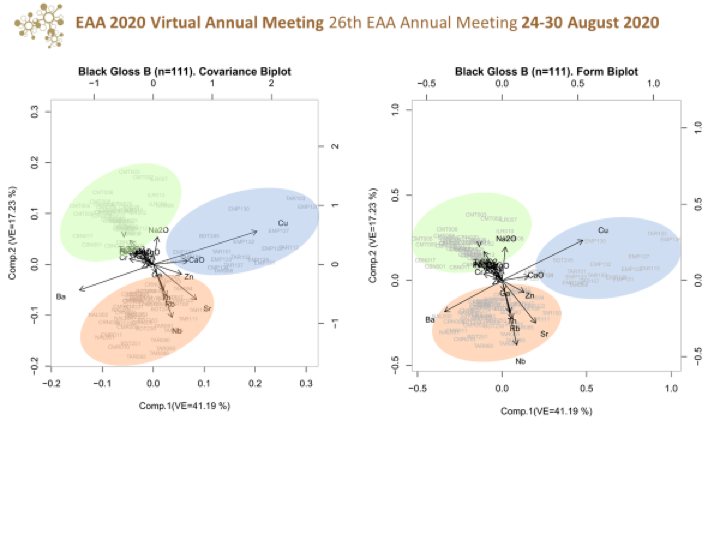
Mineralogical and microestructural characterization
In archaeometric studies, it is well-known that the main technical division between ceramics is that of calcareous and low calcareous. It has been established since the 1970s, which minerals, the microstructure, and the state of sintering and vitrification that the pottery develops depending on their low calcareous, calcareous or highly calcareous nature. Moreover, these features can be assessed by means of XRD and SEM techniques which will both be applied in our study.
During the firing process, ceramics undergo mineralogical phase transformations and densification of the microstructure depending on their composition (at the atomic, mineralogical and petrological level), firing temperature, the duration of firing, and the firing atmosphere. From those variables, only the composition can be partially determined. Firing temperature and firing atmosphere can only be tentatively estimated after the evaluation of the possible changes undergone for a given composition. However, there is no way to estimate, for ancient pottery, the duration of firing and, because of that, only the equivalent firing temperature (EFT) can be estimated. The construction of mineralogical scales according to phase transformation and the evaluation of the sintering stage during densification provide information to estimate the EFT. This is the method by which we will estimate the temperature, by studying the XRD diffractograms together with the SEM study.
Mineralogical characterization of all individuals is performed by means of X-ray diffraction (XRD). The previously prepared powder specimens were manually side-loaded and pressed with frosted glass in a cylindrical sample holder of 27 mm diameter and 2.5 mm in height (PW 1811/27). Measurements were made using a Bragg-Brentano geometry diffractometer PANalytical X’Pert PRO MPD Alpha-1 (radius = 240 mm) using the Ni-filtered Cu K radiation ( = 1.5418 Å) at a working power of 45 kV and 40 mA, equipped with an X'Celerator detector (active length = 2.122°).
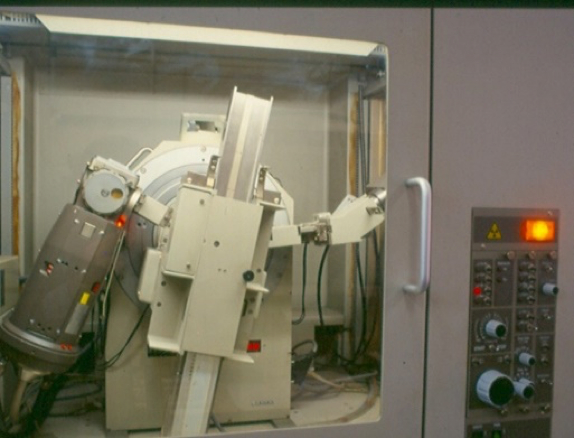
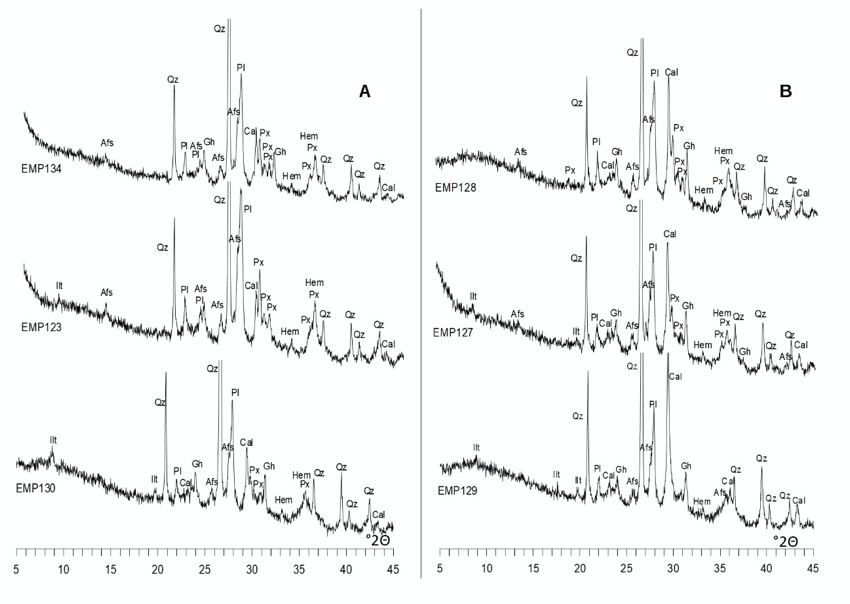
Microestructural observations
A subsample of the samples previously analyzed is always sampled for study under the scanning electron microscopy (SEM), according to the stratification revealed by XRF and XRD analysis in terms of meaningful compositional groups and mineralogical fabrics and availability of specimens. SEM observations were performed on cross-section fresh fractures passing through the oro-aboral axis of the body wall in order to observe the microstructure, to estimate the degree of sintering and the vitrification state of the matrix, and to enable microanalysis of interesting features.
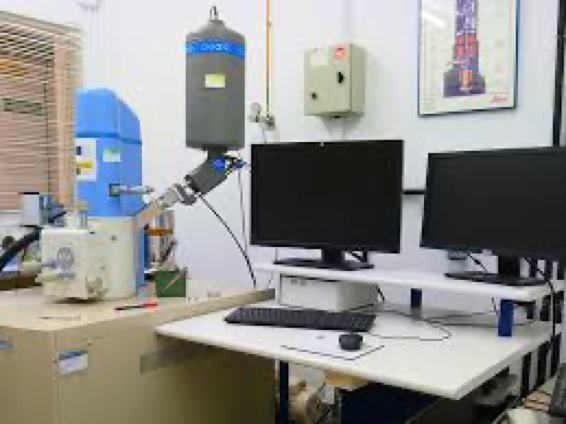
Just to give an example, in the image below, the left picture is a matrix magnified 22000 times of the sample CBN029 (Etrurian). To the right, the gloss of the studied sample CBN029 (x2000) can be seen. The matrix shows an initial/extensive vitrification microstructure. The gloss exhibits a thicknesses between 10 - 15 μm, and most of the many inclusions correspond to iron oxyde particles, and show a regular adherence to the matrix.
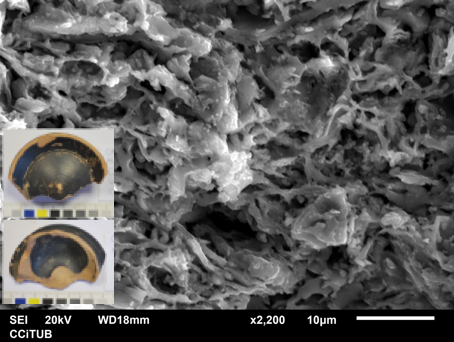
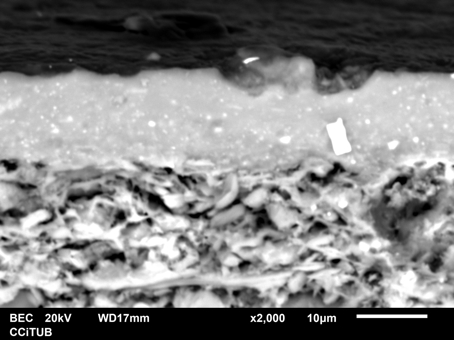
While our project has just started, you can seen some of our recently published results applying the aforementioned analytical methods here.